石英玻璃是由二氧化硅单一组分构成的特种工业技术玻璃,具有普通玻璃无可比拟的一系列优异性质,被新材料领域专家誉为“玻璃之王”,是现代信息产业、光学、光伏、半导体等国家战略性新兴产业和航空航天等国防领域的重要基础性材料。
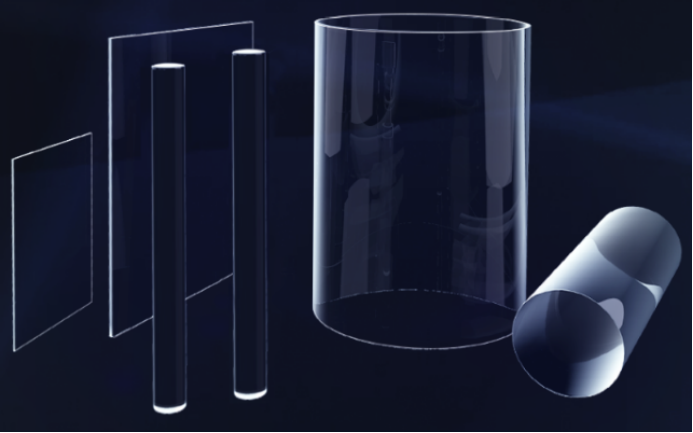
纯净的石英玻璃由单一的二氧化硅(SiO2)成分构成,石英玻璃中的Si-O键呈短程有序、长程无序的排列状态,由于Si-O键的键能较强且较为稳定,因此石英玻璃具有较高的软化温度、极佳的光谱透过性、极低的热膨胀系数和电导率、极高的化学稳定性、耐辐照性以及在极端条件下较长的工作寿命等特点。
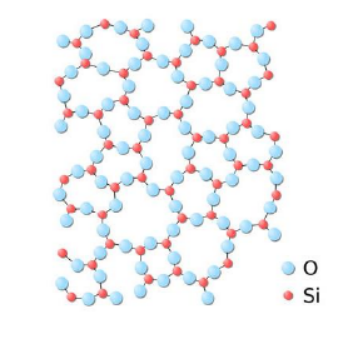
石英玻璃具有一系列优异的光学性能。与普通玻璃相比,高纯石英玻璃具有从远紫外(160nm)到远红外(5μm)极宽光谱内的良好透过性,这是一般光学玻璃所不具备的。优异的光谱透过性和光学均匀性使得石英玻璃广泛应用于半导体光刻和精密光学器件领域。此外,石英玻璃具有良好的耐辐照性能,耐辐照石英玻璃已经广泛用作“神舟”系列宇宙飞船的窗口材料,“天宫”系列空间实验室关键部件的防护罩等。
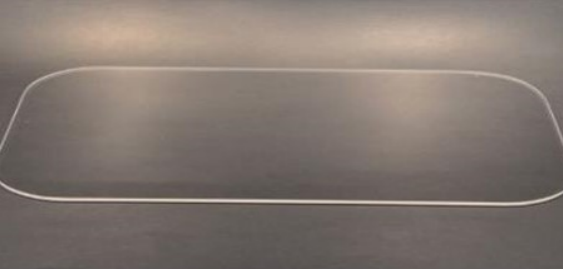
石英玻璃和普通玻璃类似,属于脆硬材料。与普通玻璃相同,石英玻璃的强度参数受很多因素影响,包括表面状态、几何形状和测试方法等。透明石英玻璃的抗压强度一般为490~1960MPa,抗拉强度为50~70MPa,抗弯强度为66~108MPa,抗扭强度约为30MPa。石英玻璃是优良的电绝缘材料。与普通玻璃相比,石英玻璃有着较高的电阻率,常温下石英玻璃的电阻率高达1.8×1019Ω∙cm。此外,石英玻璃有着较高的击穿电压(约为普通玻璃的20倍)以及较低的介电损耗。石英玻璃的电阻率随着温度升高略有下降,不透明石英玻璃的电阻率低于透明石英玻璃。由于石英玻璃内部几乎全部为较强的Si-O键作用,它的软化温度非常高,长期工作温度可达1000℃。另外石英玻璃的热膨胀系数是常见工业玻璃之中最低的,其线膨胀系数可达5×10-7/℃,经过特殊处理的石英玻璃甚至可以达到零膨胀。石英玻璃还具有非常好的抗热振性,即在短时间内反复经历极大的温差也不会开裂。这些优良的热学特性使得石英玻璃在高温和极端工作环境中有着其他玻璃不可替代的地位。
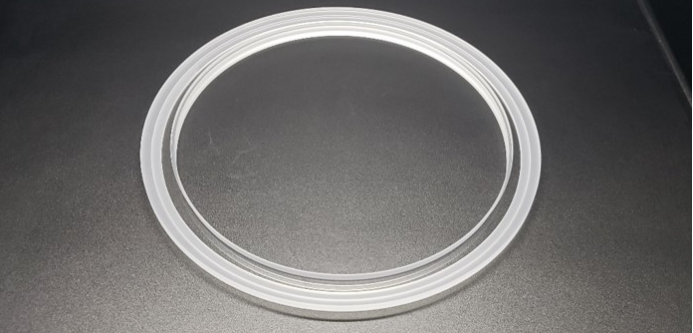
高纯的石英玻璃可以应用在半导体行业的芯片制造、光纤制造的辅材、工业高温炉的观察窗、大功率电光源以及航天飞机表面充当隔热层等。极低的热膨胀系数还使得石英玻璃可以应用于精密仪器、大型天文望远镜的镜头材料等。石英玻璃的化学稳定性非常好。不同于其他的商业玻璃,石英玻璃对水有着极高的化学稳定性,因此可以应用在对水的纯度要求极高的水蒸馏器中。石英玻璃具有优良的耐酸性和耐盐性,除氢氟酸、磷酸和碱性盐溶液外,与大多数酸和盐溶液都不发生反应。与酸和盐溶液相比,石英玻璃的耐碱性较差,在高温下会与碱溶液反应。除此之外,石英玻璃和大多数氧化物、金属、非金属以及气体等在常规温度下都不反应。极高的纯度和良好的化学稳定性使得石英玻璃可以应用在半导体制造业等对生产条件要求较高的环境中。
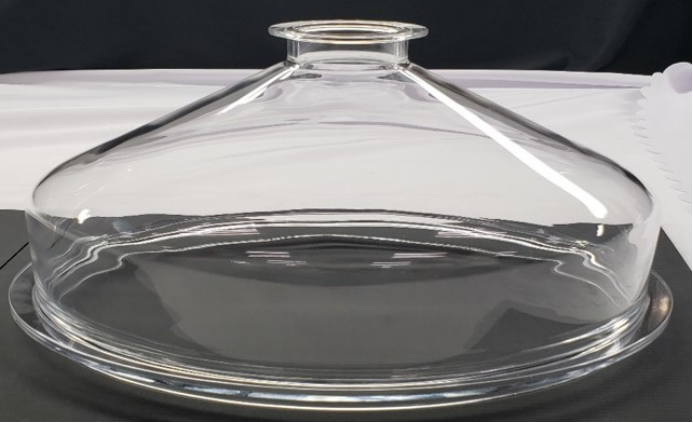
石英玻璃的制备方法可以分为两大类。第一类是以天然石英晶体或硅石为原料进行熔制得到,称为天然石英玻璃。根据热源和工艺的不同可以将第一类方法细分为电熔法,气炼法,等离子体熔制法等。第二类是以含硅化合物(包括卤化硅,氢化硅及有机硅等)为原料通过化学反应合成得到,称为合成石英玻璃,根据反应原理的不同可以将第二类方法分为:等离子体化学气相沉积法(PCVD)、火焰水解沉积法(FHD)、溶胶-凝胶法。
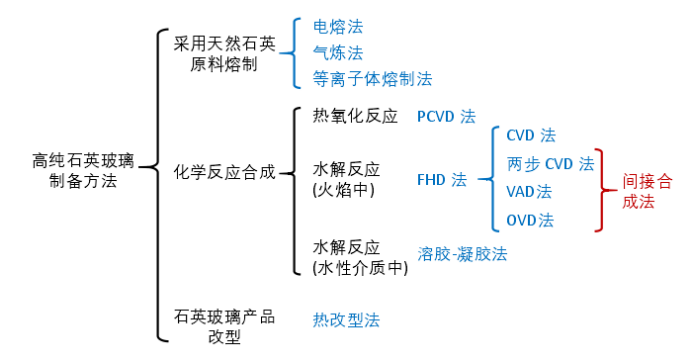
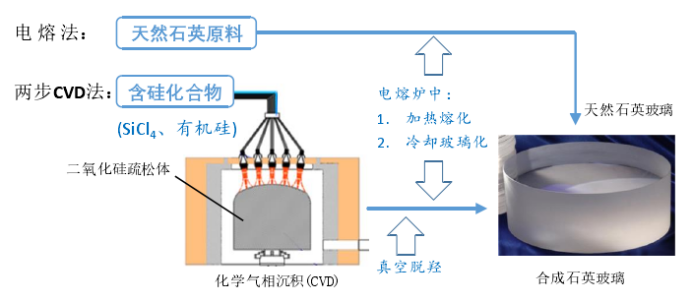
在电熔法中,首先通过电加热(电阻加热或电磁感应加热)将坩埚内的粉末状石英原料进行熔化,随后经过快速冷却的玻璃化过程形成石英玻璃。采用电熔法制备的石英玻璃,其品质主要取决于原料的纯度。石英原料中的金属杂质通常很难去除,因此电熔石英玻璃中的金属杂质一般含量较高且难以控制。通过烘干可以有效去除石英粉料中的水分,因此采用电熔法可以制备出羟基含量较低的石英玻璃。两步CVD法,即“两步法”气相沉积法,该方法可分为两步,第一步是在较低的温度下进行水解反应,此时生成的SiO2颗粒呈烟灰状,SiO2颗粒沉积在基板上首先得到SiO2疏松体,该疏松体是一种多孔结构的无定形SiO2。第二步将制得的SiO2疏松体转移到高温加热炉内进行脱羟,然后经过烧结和冷却过程最终制得石英玻璃。采用两步化学气相沉积(CVD)法制备高纯石英玻璃锭是国内近年来着力发展的新技术,其优势在于可以生产出低羟基或羟基含量可控的石英玻璃,从本质上避免了金属杂质的引入,因此具有广阔的发展前景。但是两步CVD法目前仍面临着一系列技术挑战,主要表现在制备工艺不成熟、对制备过程中的关键科学问题认识不足等,限制了其成为工业中制备石英玻璃的主流技术。此外,石英玻璃制备工业还存在着玻璃气泡缺陷以及产品热改型过程难以控制等难题,造成石英玻璃的质量无法得到有效保障。
声明:转载此文是出于传递更多信息之目的。若有来源标注错误或侵犯了您的合法权益,请作者持权属证明与本网联系,我们将及时更正、删除,谢谢。
来源:粉体网
管理员
该内容暂无评论